Why plastic extrusion is ideal for mass production
Why plastic extrusion is ideal for mass production
Blog Article
Recognizing the Essentials and Applications of Plastic Extrusion in Modern Manufacturing
In the realm of modern manufacturing, the strategy of plastic extrusion plays a crucial role. Unraveling the fundamentals of this process reveals the true versatility and possibility of plastic extrusion.
The Principles of Plastic Extrusion Refine
While it may appear facility, the basics of the plastic extrusion procedure are based on relatively straightforward concepts. It is a production process where plastic is thawed and after that formed right into a continuous profile through a die. The raw plastic material, commonly in the form of pellets, is fed right into an extruder. Inside the extruder, the plastic is subjected to warmth and pressure, creating it to thaw. The liquified plastic is then compelled with a shaped opening, understood as a die, to develop a long, constant item. The extruded item is cooled down and afterwards reduced to the preferred size. The plastic extrusion procedure is thoroughly utilized in different industries as a result of its effectiveness, cost-effectiveness, and flexibility.
Different Kinds of Plastic Extrusion Techniques
Structure upon the standard understanding of the plastic extrusion process, it is required to explore the numerous strategies associated with this production approach. The 2 main strategies are profile extrusion and sheet extrusion. In profile extrusion, plastic is melted and created into a continuous account, commonly utilized to develop pipes, poles, rails, and home window frames. On the other hand, sheet extrusion creates huge, level sheets of plastic, which are normally more refined into items such as food packaging, shower curtains, and cars and truck components. Each method calls for specialized equipment and precise control over temperature and pressure to make sure the plastic preserves its form throughout cooling. Comprehending these methods is vital to using plastic extrusion effectively in contemporary production.
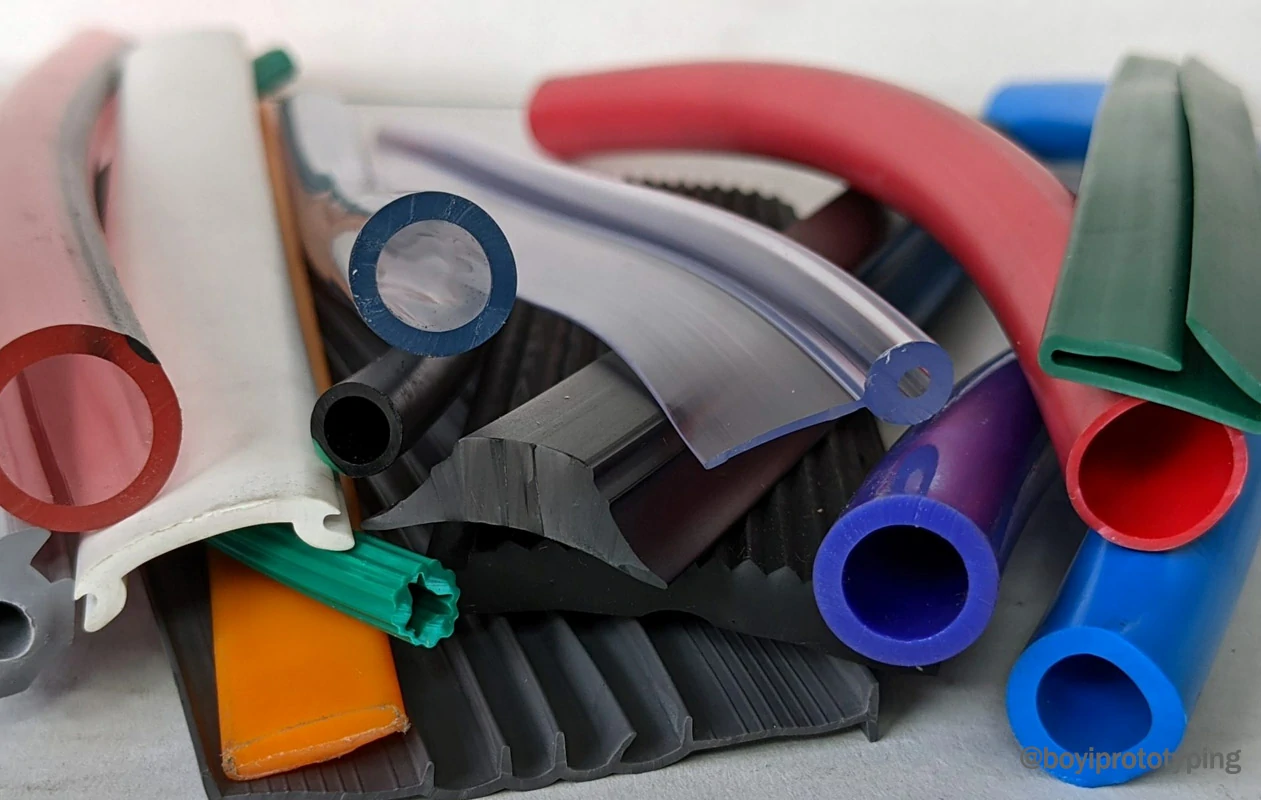
The Duty of Plastic Extrusion in the Automotive Sector
An overwhelming majority of parts in contemporary vehicles are products of the plastic extrusion procedure. Plastic extrusion is primarily used in the production of various auto parts such as bumpers, grills, door panels, and dashboard trim. Hence, plastic extrusion plays an essential duty in automotive manufacturing.
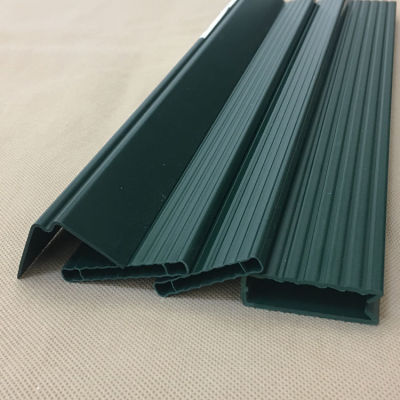
Applications of Plastic Extrusion in Consumer Item Manufacturing
Beyond its significant effect on the automobile industry, plastic extrusion verifies equally effective in the realm of customer goods producing. The adaptability of plastic extrusion enables suppliers to design and generate intricate shapes and dimensions with high precision and performance. The versatility, versatility, and cost-effectiveness of plastic extrusion make it a recommended choice for several consumer goods makers, contributing dramatically to the sector's development and development.
Environmental Effect and Sustainability in Plastic Extrusion
The prevalent use plastic extrusion in producing invites analysis of its eco-friendly effects. As a procedure that frequently uses non-biodegradable materials, the ecological influence can be considerable. Power usage, waste production, and carbon exhausts are all concerns. Industry developments are boosting sustainability. Reliable equipment minimizes energy usage, while waste management systems recycle scrap plastic, decreasing basic material demands. Additionally, the their website growth of biodegradable plastics offers a more environmentally friendly choice. Despite these improvements, even more advancement is needed to alleviate the environmental footprint of plastic extrusion. As culture leans towards sustainability, makers need to adapt to continue to be feasible, emphasizing the significance of constant study and innovation in this area.
Conclusion
In verdict, plastic extrusion plays an essential function in modern-day production, especially in the automobile and durable goods sectors. Its versatility enables the manufacturing try this out of a large range of components with high precision. Its capacity for recycling and advancement of naturally degradable materials offers an appealing avenue towards sustainable techniques, therefore attending to environmental worries. Comprehending the fundamentals of this process is key to enhancing its applications and advantages.
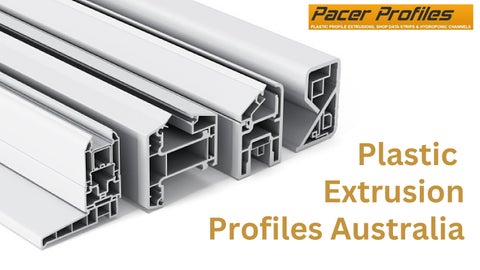
The plastic extrusion procedure is extensively used in various industries due to its adaptability, efficiency, and cost-effectiveness.
Building upon the basic understanding of the plastic extrusion procedure, it is essential to check out the numerous strategies entailed in this manufacturing method. plastic extrusion. In contrast, sheet extrusion creates huge, level sheets of plastic, site which are usually further refined right into products such as food packaging, shower curtains, and cars and truck parts.An overwhelming majority of components in contemporary automobiles are products of the plastic extrusion procedure
Report this page